AGV and AMR systems automate transportation processes efficiently and safely. Their implementation requires integrated, certifiable hardware and software solutions. To simplify development, manufacturers such as NXP© and MicroSys Electronics offer suitable platforms and tools.
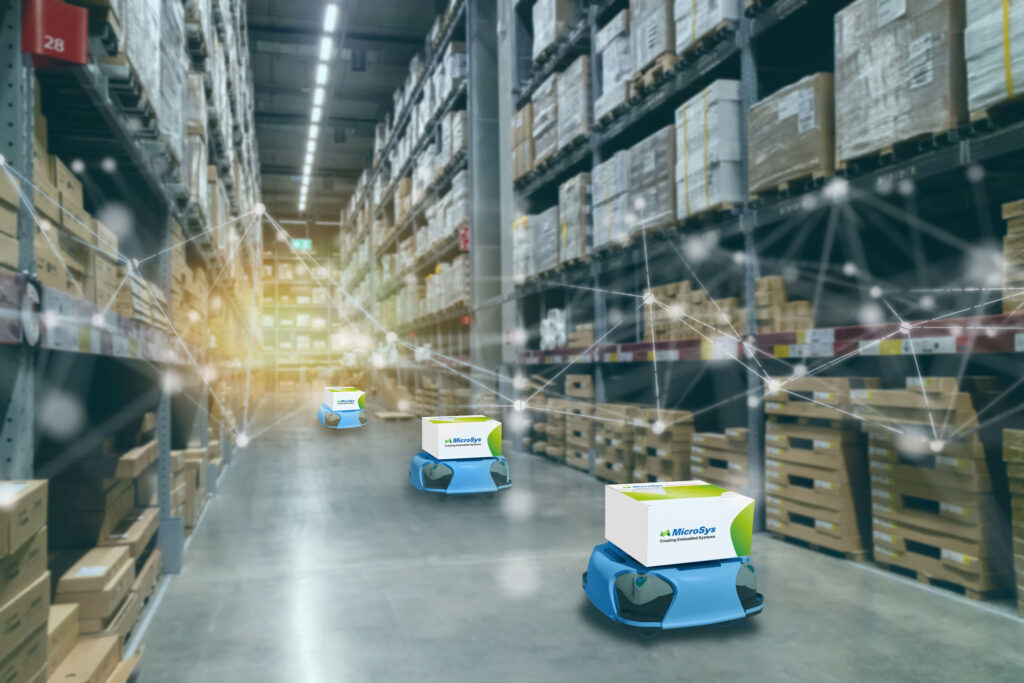
Modern robotic applications such as Automated Guided Vehicles (AGVs) and Autonomous Mobile Robots (AMRs) ensure safe, precise, and automated material handling, especially in industries like manufacturing, logistics, and food processing. These systems help relieve the workload of employees and mitigate the shortage of skilled labor. They can also be flexibly integrated into existing systems. While AGVs follow predefined routes using tracks and markers, AMRs rely entirely on onboard sensors, real-time processing, and AI to interpret their surroundings and make autonomous decisions.
AGVs and AMRs are characterized by intelligent navigation and localization capabilities, advanced sensor fusion, and high-speed communication between components. To meet these demands, modern AGV/AMR systems require various components such as dedicated computing cores, Global Navigation Satellite System (GNSS) modules, and advanced network interfaces. Conventional computing architectures are no longer sufficient. Edge processors handle tasks such as image processing, motion control, and other local computations. However, their integration can be complex, often resulting in intricate hardware and software architectures.
Integration Challenges
The interplay of various components such as
- perception sensors,
- image sensors,
- LiDAR, and
- Radar
is essential to ensure safe movement and navigation of AGVs/AMRs. Achieving minimal latency in data transmission is critical. This requires seamless interaction between hardware, software, and middleware. To meet these requirements, manufacturers like MicroSys Electronics offer future-ready hardware components such as system-on-modules (SoMs), operating systems, and frameworks for real-time control.
Reducing Design Complexity
Preconfigured SoMs reduce design complexity by providing key components in an application-ready module. A module well-suited for AGV/AMR systems is the miriac® MPX-S32G399A from MicroSys. Applications previously based on its predecessor, the miriac® MPX-S32G274A, can now be upscaled to the new module and benefit from increased CPU performance. Both modules share compact dimensions of 82 mm x 50 mm, simplifying replacement.
To further reduce design complexity, developers can use a carrier board that, combined with the SoM, forms the single-board computer (SBC) miriac® SBC-S32G399A. The SBC offers developers pre-integrated software and comprehensive design-in services. Advanced CPU interfaces available through the SBC ensure maximum connectivity for applications.
In addition to the miriac® MPX-S32G399A, the miriac® MPX-S32Z2 can be used to control external peripherals such as image, LiDAR or radar sensors – as used in AGV/AMR – in real time and to process and analyze recorded sensor data directly. It is based on the NXP© S32Z2 CPU, which provides outstanding real-time capabilities. For this, developers only need to use a second carrier board, which combines and expands the single-board computer MPX-S32Z2 with the SBC MPX-S32G399A.
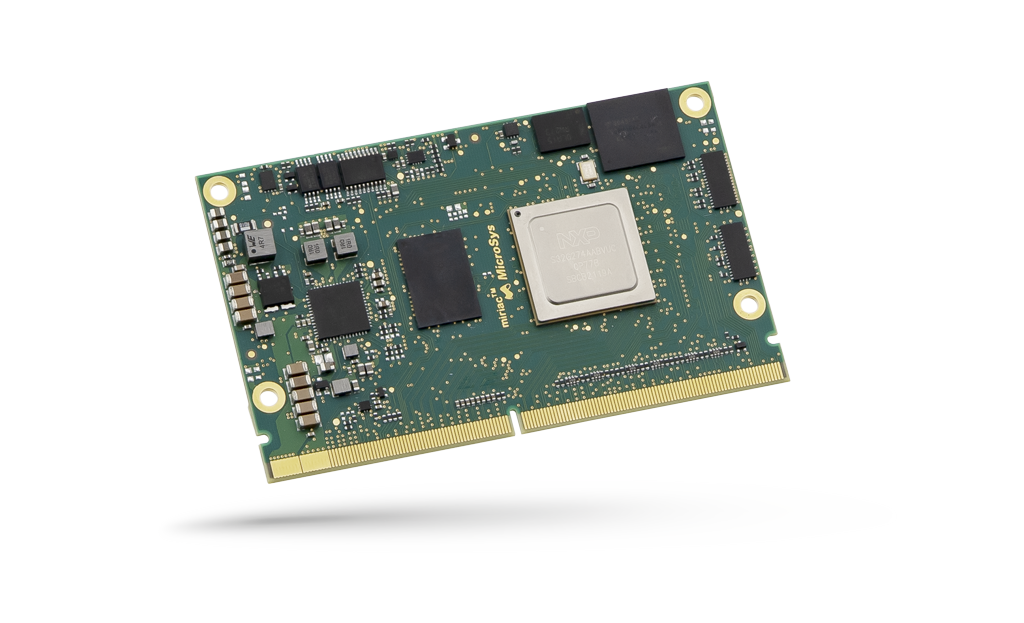
High-Efficiency Real-Time CPU
The miriac® MPX-S32G399A SoM is based on NXP’s© S32G399A processor, which combines ASIL-D safety with high-performance real-time and application processing, along with extensive network acceleration. The S32G3 CPU supports modern vehicle architectures such as service-oriented gateways, vehicle computers, domain controllers, zonal processors, safety processors, and more.
It features eight Arm® Cortex®-A53 cores running up to 1.3 GHz, optionally operating in lockstep mode for enhanced safety. Four Arm® Cortex®-M7 dual-core lockstep cores supplement application cores with functionality for safety-critical real-time tasks. The CPU is supported by up to 4 GB LPDDR4-32-bit memory at 3200 MT/s, 64 MB QSPI flash, and up to 32 GB eMMC storage. The integrated Hardware Security Engine (HSE) provides secure boot functionality, and the Low Latency Communication Engine (LLCE) accelerates CAN, LIN, and FlexRay message processing. NXP© guarantees long-term availability with a product lifecycle of up to ten years – or even 15 years for some applications –significantly enhancing future viability.
To further increase real-time performance, AI accelerators such as the Hailo-8 AI processor can be integrated via the onboard M.2 connector, enabling faster data processing and comprehensive sensor fusion.
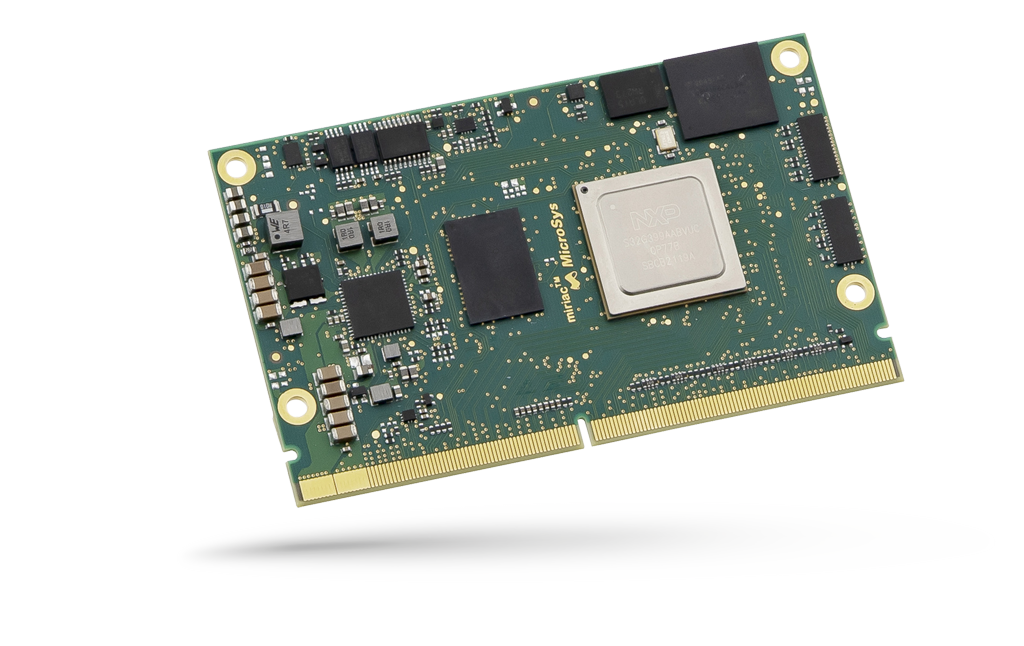
Module Meets Highest Connectivity Demands
To meet modern AGV/AMR communication requirements, the SBC offers a wide range of Ethernet interfaces, some with Time-Sensitive Networking (TSN) support, including:
- 1x 1GbE
- 1x 1000BASE-T1
- 1x 100 Mb
- 6x 100BASE-T1
In addition, MicroSys provides interfaces such as USB 2.0, 18x CAN-FD, 8x LIN, 2x FlexRay, GPIOs, and JTAG. The automotive-specific SJA1110 switch is also included in the comprehensive interface support.
The module can withstand harsh environments ranging from 0 to +70 °C – and from -40 to +85 °C in extended temperature ranges – significantly reducing development risks. Its modularity shortens time-to-market, helping developers save time and costs. Integrated security features allow compliance with industry-specific safety and regulatory standards.
MicroSys also offers a comprehensive development kit with accessories such as power supply and heat sink for quick prototyping and application development. This kit accelerates evaluation and integration of the SoM and provides developers with extensive support including documentation, reference designs, and software tools.
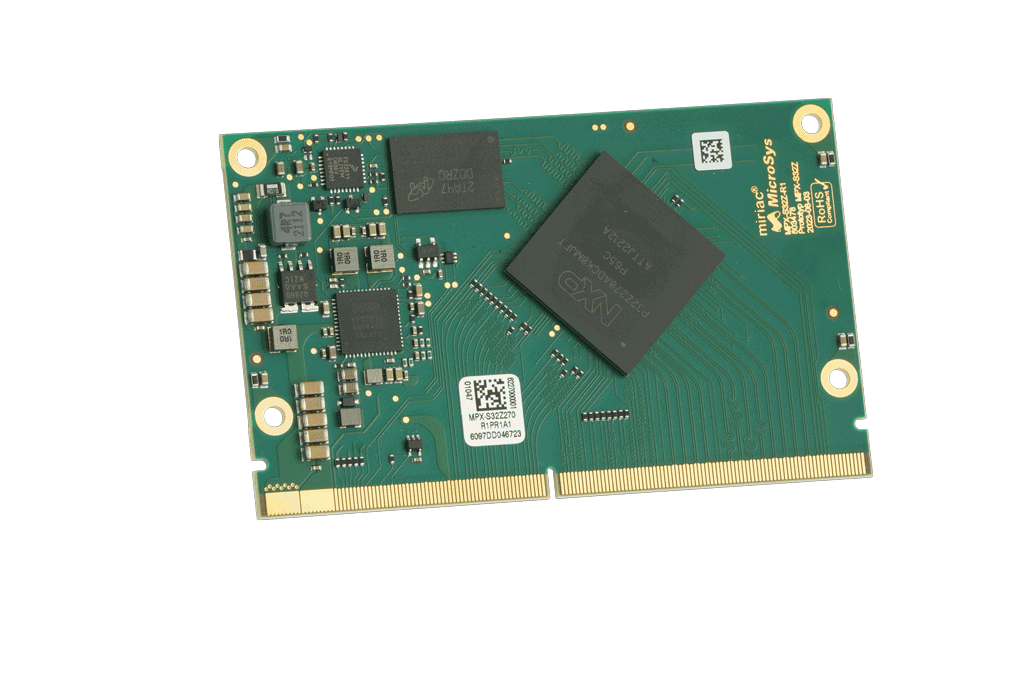
Advantages over SMARC
Compared to an open computer-on-module standard like SMARC, MicroSys can fully leverage the performance of the NXP© CPU with its proprietary standard. Not all CPU interfaces can be made externally available via SMARC, as the standard only supports certain pinouts.
In contrast, the MicroSys SoM exposes all critical interfaces – such as all Ethernet and CAN ports –enabling a scalable number of interfaces and maximum CPU performance at the connector. It also offers optional CPU monitoring via a supervisor.
Expert Software Integration
Besides hardware, the right software plays a critical role for AGVs/AMRs, supporting functions such as:
- Navigation
- Object detection
- Route planning
- Power management
These functions require real-time data transmission and processing for rapid response. The software must also meet safety-critical certification standards.
To ease this challenge for developers, MicroSys provides an application-ready Linux operating system on its platform. Developers can therefore fully concentrate on their application. MicroSys can also offer support from qualified partners for bare-metal or QNX programming.
Comprehensive software integration enables AGVs/AMRs to operate seamlessly, safely, and efficiently, with optimal interaction between sensors, control systems, and communication interfaces. It also enhances scalability, facilitates updates, and allows quick adaptation to new processes or environments.
Summary
AGVs and AMRs are increasingly used to boost efficiency, flexibility, and operational safety in industry, logistics, and transport. However, developing these systems poses challenges such as real-time processing, stringent safety certifications, and complex software integration.
Manufacturers like NXP© and MicroSys support developers with prevalidated hardware, extensive security features, and optional middleware—significantly reducing development effort and risk. With comprehensive software integration, AGVs/AMRs benefit from greater scalability, improved data availability, and safe, autonomous operation.