Which NXP processor based platform are you looking for? Check out our NXP Layerscape, NXP QorIQ, and NXP S32 processor based System-on-Modules, SBCs and embedded systems. We are sure that you will find an embedded computing platform that suits best for your next generation of medical devices!
The Foundation for Driverless Excavation
In the future, not only cars, buses or delivery vans will act autonomously. MicroSys used task-optimized system-on-modules designed in-house to create a ready-to-install, modular autonomous control system facilitating mobile machinery automation. With only 60 W power consumption, the Autonomous Control Unit (ACU) does not require active cooling. It is perfectly suited for many years of operation in harsh conditions.
The phrase “autonomous driving” is frequently used in context with cars, buses, trucks or delivery vans in driverless motion on public roads. These are, however, by no means the only application for these complex navigation methods. Automotive, self-propelled agricultural or construction machines and material handling equipment also come with a considerable potential for automation.
Highly automated machinery
The task of automating automotive machinery differs considerably from creating driverless vehicles for use in road traffic. During their normal operation, agricultural or construction machinery typically do not move on public roads but in segregated areas with no access for uninvolved people. This involves navigating not on mostly level surfaces but driving in rough terrain. As the terrain, which is the Basis for course verification, changes due to the progress of the construction work, it frequently needs to be mapped anew. Furthermore, the autonomous activities should not be limited to driving but also include load handling and transfer.

For autonomously navigating and acting self-propelled machinery on our fields and construction sites to become commonplace, a number of basic prerequisites need yet to be created. Germany’s Federal Ministry of Economy and Climate Protection supports this industry’s transformation. Its KoPa 35c funding program mainly benefits mobile machinery manufacturers and suppliers.
Within the cooperative project POV.OS (Professional Vehicle Operating System), an innovative automation platform for functionalizing mobile machinery is being designed. It comes in the form of an open architecture comprising modular hardware and software system components. This constitutes a cross-application platform to be used to specify and implement application-oriented functionalities for automation, assistance and autonomous driving.
Modularly economical
Automotive machines are manufactured in far smaller quantities than most automobiles. Full-custom designs of the central control electronics would not be economically feasible for their manufacturers. They prefer commercially available so-called COTS platforms (for commercial off-the-shelf). These allow design engineers to create individual solutions without the need to deal with individual components.
As a Gold Partner of the processor manufacturer NXP, MicroSys Electronics GmbH (MicroSys) designs system-on-modules (SoM), constituting an effective means for this design method. In a small form factor, these assemblies integrate a microprocessor and storage as well as connectivity and all other components required for application development and certification. Used as central computing units with standardized interfaces, SoMs help manufacturers of professional mobile machinery cut thee design cycles of their products. To implement application-specific functionalities, SoMs are mounted on custom carrier boards. These also supply the modules with power and translate input and output signals into industry-specific formats and protocols.
A strong heart
MicroSys designed the miriac® MPX-LX2160A SoM not solely for mobile machines but for a broad spectrum of applications with similar performance and safety requirements. The module is based on the LX2160A, currently NXP’s most powerful embedded multi core processor featuring 16 Arm® Cortex®-A72 kernels. Its 32 GB soldered DDR4 RAM can be extended to a maximum 128 GB. The module’s processor-integrated Ethernet controller facilitate a highly performant high-end communication with up to 100 Gbit/s Ethernet and integrated 122 Gbit/s Layer 2 Ethernet Switching. This allows integration of all networked tasks within a vehicle, including GigEVision camera systems.
The SoM has four PCIe 3.0 interfaces to accommodate the large SSD mass storage this calls for. The integrated security engine of the LX2160A processor facilitates full data encryption all the way to the maximum data transfer bandwidth. It uses secure boot to ensure loading only software from certified sources, for instance in case of updates. The miriac® MPX-LX2160A SoM is specified for use over a -40° C to +85° C temperature range. With at least 15 years availability, it provides mobile machine manufacturers with a good supply security for its core component.
Task-optimized carrier board
It takes more than just a central processor module. Many mobile machine manufacturers lack the required expertise or capacities to build a comprehensive solution around it. In the design of a task, but not customer specific control system platform for mobile machines, MicroSys used insights gained within the POV.OS project. The Bavarian manufacturer also falls back on experiences from many years of fulfilling requirements of this industry.
The COTS MicroSys carrier specified in the POV.OS context features three M.2 slots and can be fitted with a miriac® MPX-LX2160A, an FPGA accelerator module, up to three SSD RAM modules or one or two Hailo-8™ AI processor modules. In case a separate safety island is required in the context of a project, MicroSys offers an extension based on the miriac® MPX-S32G274A or miriac® MPX-S32G399A. This provides the solution with additional computational power for complex tasks as well as an independent instance.
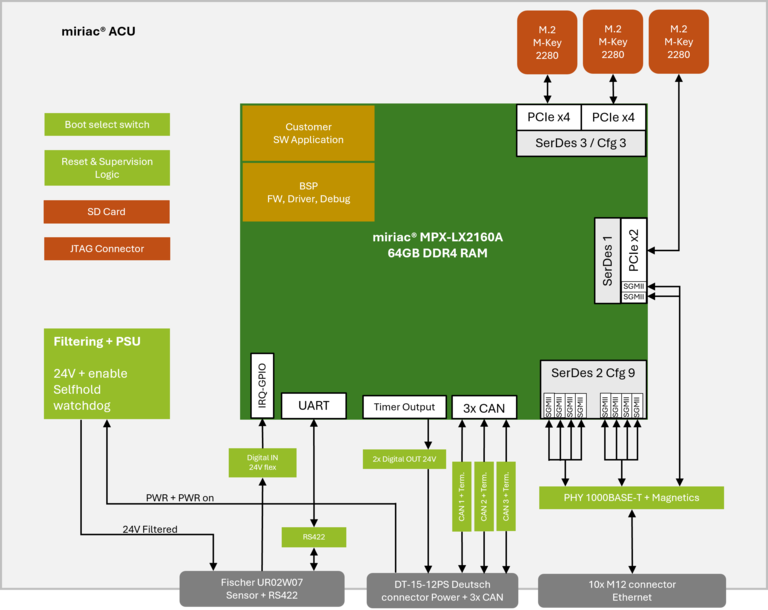
Ready-to-install system
What makes the electronics a ready-to-install, ruggedized system is its purpose-designed housing rated IP68 for dust and water resistance. In its standard form, it has M12 connectors for ten GB Ethernet interfaces and a rugged Fischer connector for serial data buses. A Deutsch connector for the power supply also provides connectivity for three CANbus lines. Aside of protecting the electronics, the housing also serves as a heat sink. It transfers most of the heat through its base plate to the vehicle frame. A smaller portion of the thermal energy radiates into the ambient air through gills on the upper side of the device.
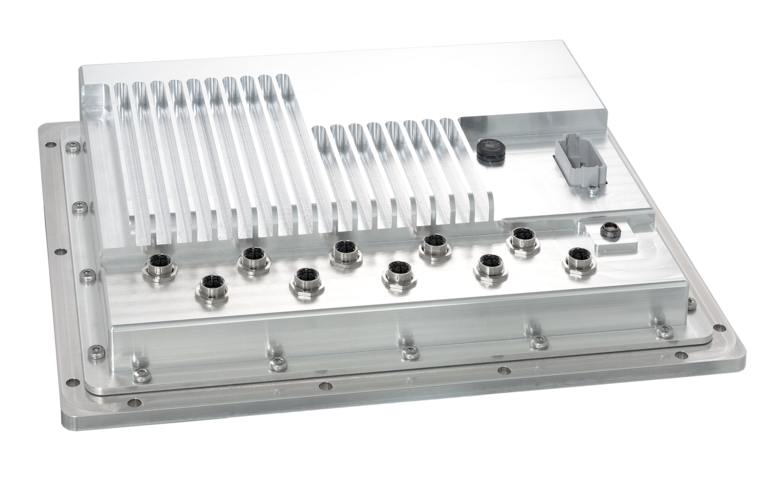
In spite of its exorbitantly high computing power of the fully loaded unit and its multiple interfaces, MicroSys managed to limit its power consumption to 60 Watt, creating a system without any moving parts and without the need for active cooling. “All tests confirm sufficient cooling up to ambient temperatures of at least 55° C”, says Jörg Stollfuß, Application Engineer at MicroSys Electronics GmbH. “With the new Autonomous Control Unit based on the miriac® MPX-LX2160A SoM, we can offer mobile machine manufacturers a ready-to-install control and automation system for their products.”
“With the new Autonomous Control Unit based on the miriac® MPX-LX2160A SoM, we can offer mobile machine manufacturers a ready-to-install control and automation system for their products.”
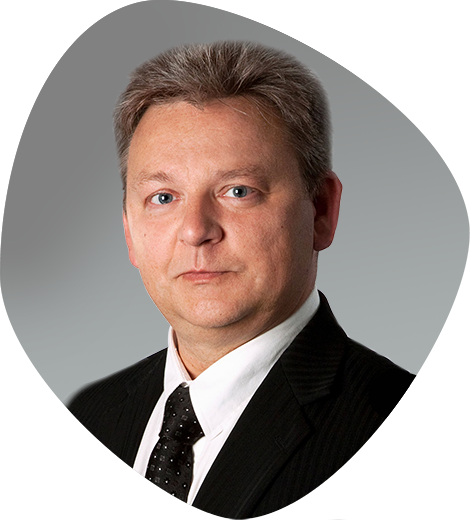
Publications
Download
Learn more about our products and services
Talk to our medical computing experts!
Curious about our NXP processor based embedded computing platforms for medical devices and our system design services? Just ask us! We can't wait to hear from you to help you personally.