Which NXP processor based platform are you looking for? Check out our NXP Layerscape, NXP QorIQ, and NXP S32 processor based System-on-Modules, SBCs and embedded systems. We are sure that you will find an embedded computing platform that suits best for your next project!
Rugged Connectivity Giant
Liebherr Mining, a leading manufacturer of dump trucks and hydraulic excavators for surface mining, makes its mobile machines part of the Internet of things to facilitate even more economic operation and maintenance. For this, the long-standing, family-operated enterprise used a miriac® system-on-module from MicroSys, integrated in a custom carefree system solution.
In many areas of day-to-day life and the economy, we depend on mineral raw materials retrieved from the earth’s crust in mines. As these are not renewable, continuous consumption reduces their availability. This makes ensuring high efficiency in mining a necessity.
Rock stars for the mining industry
The German construction machinery manufacturer Liebherr is aware of the extreme challenges the mining industry is facing. In Colmar, France, and Newport News, Virginia (USA), the Liebherr Mining product segment produces excavators and dump trucks with up to 800 tons service weight and up to 47,5m3 bucket capacity for raw material extraction in surface mining. Designed to meet the specific requirements of the mining environment, these are powered by Diesel engines or electric motors.
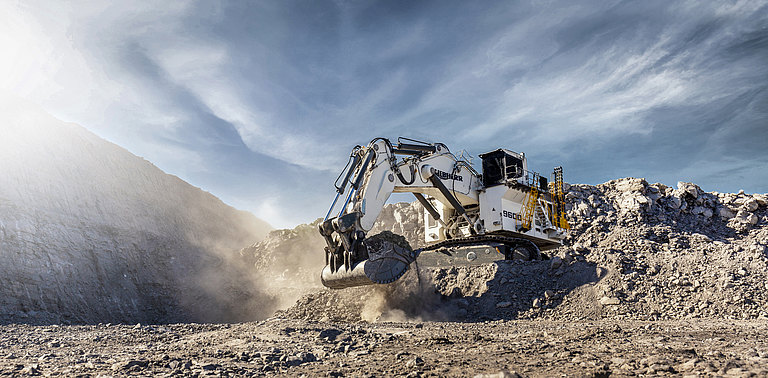
The company draws from more than 50 years of experience. With high quality, reliability and innovative technologies, its equipment facilitates time and cost-efficient mining projects in the harshest conditions. To ensure high-grade products, Liebherr produces the mining excavators with a high in-house production depth. Quality components designed and manufactured in-house such as control systems and electronics or turning and traction drives enhance the reliability and performance of the machines that are in high demand across the globe and used on all continents.
Data acquisition and communication
One of the goals of present-day mining technology is to keep the impact on nature at a minimum while optimizing yields and produce concise documentation of all material movements fast. Another is to ensure a high availability of the mining equipment using predictive maintenance.
In pursuit of these goals, Liebherr turned to MicroSys Electronics GmbH for the design and production of a connectivity box for use in the heavy mining machines. The company based at Sauerlach near Munich, Germany, mainly designs and manufactures miriac® system-on-modules (SoM). It is Gold Partner of NXP®, using this processor manufacturer’s Arm® Cortex® platforms to create application-ready embedded solutions. Using these SoMs, MicroSys also designs custom system solutions. These range from embedded computing platforms to real-time control hardware for mobile as well as stationary machines or high-bandwidth network and edge computing applications. MicroSys can also provide high-precision mechanical designs or help acquire certification to international standards such as IEC61508.
The connectivity box was meant to accommodate a processor module and provide a wide variety of interfaces. Its task is to acquire, concentrate and pre-process a variety of vehicle data and pass the resulting information on using existing WiFi or cellphone networks.
Embedded computing from Munich
“According to the original specification, the connectivity box should be the size of a packet of cigarettes”, Jörg Stollfuß, Field Application Engineer at MicroSys Electronics, recalls. “We actually achieved 260 x 140 x 70 millimeters.” In view of the fact that the central vehicle network SoM miriac® MPX-S32G274A alone has a size of 82 x 50 mm and the box has about 100 external contacts in several connectors, this is a respectable achievement. Even more so, if the impermeability and shock resistance requirements are taken into account as well.
The miriac® MPX-S32G274A SOM is equipped with the NXP® S32G2 processor featuring four Arm® Cortex®-A53 kernels and three Arm® Cortex®-M7 kernels with lockstep support. It communicates via 18 CAN FD interfaces and a dedicated protocol generator and numerous other interfaces such as FlexRay, Lin, SPI, Ethernet with TSN, PCI Express®, USB and I²C. Additionally, the SoM also boasts a hardware security engine for secure booting and fast security services.
Robust vehicle data acquisition
To clarify the requirements, MicroSys made a concept study determining the system architecture, mechanics and preliminary component placement. This formed the foundation for the full custom design of both the electronics and the housing of the Conbox (Connectivity Box) and for prototyping.
During the custom design of the carrier board and housing of the connectivity box, MicroSys needed to take the extreme environmental conditions during mining operations into account. The devices are screwed on to the vehicle frames. They need to operate at altitudes up to 5,500 m (18,000 ft.), withstanding temperatures from -40 to +70 ° C and vibrations up to 6 G with uncompromised functionality. They are rated IP68 for protection against dust and permanent flooding. “Only fanless equipment can meet this bundle of specifications“, says Jörg Stollfuß. “These were complemented by strict electromagnetic compatibility (EMC) requirements.
Secure data concentration
The Conbox features 4 GB memory in the shape of a soldered-on eMMC (embedded multimedia card). Serving as a batteryless backup, it facilitates up to 250 milliseconds uninterrupted operation to bridge short interruptions of the on-board power supply and to allow an orderly shutdown of the system in case of continued power failure. Settings are stored in a non-volatile 512 kB EEPROM.
The connectivity box acts as a central gateway between the vehicle bus (CAN, Ethernet) and a separate uplink box that transfers the data to the Liebherr Cloud via a safeguarded link. This mainly serves the purposes of predictive maintenance, but is also used to transmit transport data used for optimizing material movements and for efficiency monitoring.
The design of the connectivity box allows its use not only in new equipment but also for retrofitting or upgrading existing machines. This is why it can handle power supply voltages from 19 to 32 Volt. Equipped with a miriac® MPX-S32G274A processor module, it has a power consumption of about 50 Watts.
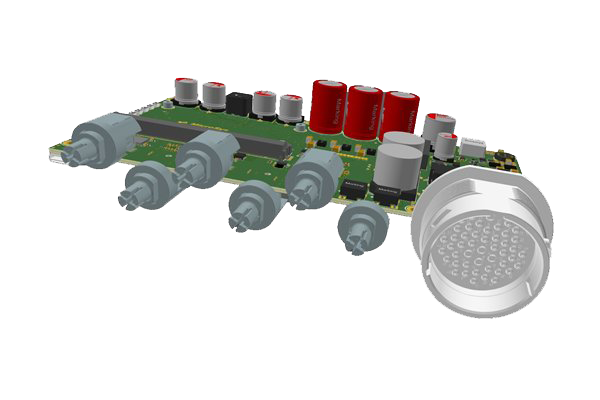
Tiny connectivity giant
In spite of its minuscule dimensions, the connectivity box offers a broad variety of connectivity options. On the vehicle side, it features eight separate CAN bus interfaces serving various parts of the vehicle itself such as engine control, excavator shovel control, etc. Via up to five Gigabit Ethernet interfaces, this data is concentrated, mostly combined and filtered as well as preliminarily stored using software designed by the vehicle manufacturer and finally passed on to the Liebherr Cloud using a vehicle-based modem.
The connectivity box is EMC-certified according to ISO13766. It also features a Gigabit Ethernet switch. Two of its six ports can be used without separate power supply lines using 15 W power over Ethernet. There are also a PCI Express interface and two serial UART interfaces. The box’s connectivity portfolio is supplemented by a GPS module for independent positioning, a USB interface for programming or updating and a WiFi module for local maintenance access using a tablet computer. This comprehensive connectivity is accessible through a 47-pin circular connector, eight X-coded M12 Ethernet connectors and a USB Type C connector.
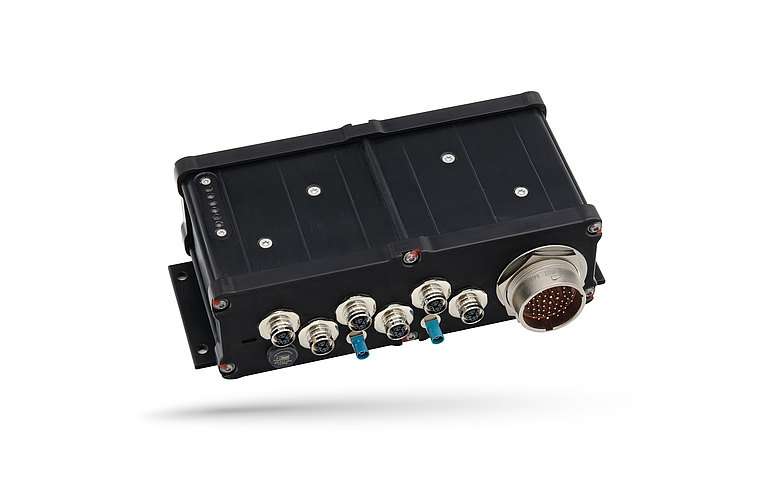
The design of the connectivity box took place in several iterations. This was due in part to the COVID pandemic and in part to new requirements formulated after prototyping. “The first preproduction prototypes have been in operation without any failures since late 2021”, says Frédérique Muller, Manager R&D Electrics, Electronics and Cloud Services at Liebherr Mining Equipment. “Final acceptance can be expected by the end of 2024.” This will be followed by serial production with about 150 connectivity boxes per year, plus some for retrofit.
“According to the original specification, the connectivity box should be the size of a packet of cigarettes. We actually achieved 260 x 140 x 70 millimeters.”
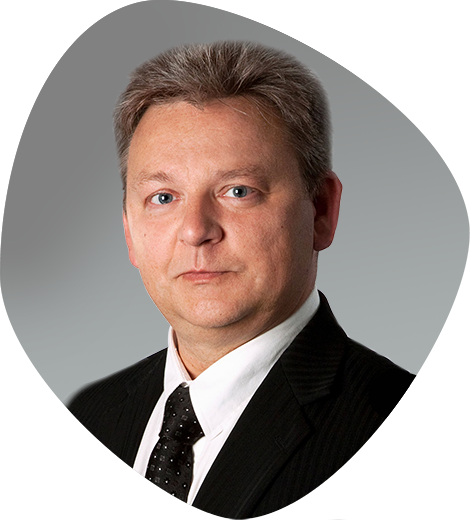
“With this Autonomous Control Unit based on the miriac® MPX-LX2160A SoM, MicroSys as a ready-to-install, modular and scalable hardware platform for the automation mobile machinery, System design engineers can fully concentrate their focus on software design.”
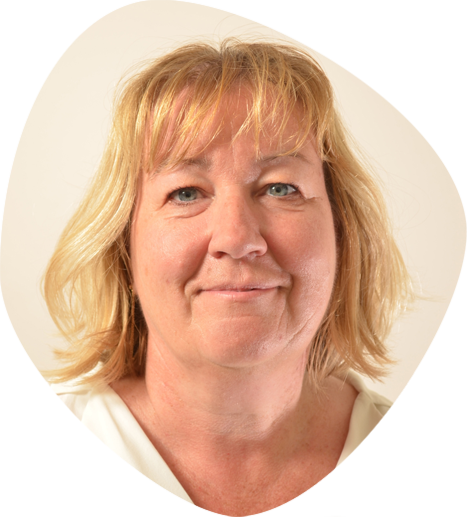
About Liebherr:
The Liebherr group is a technology business with a broadly diversified product spectrum managed by the Liebherr family. Ranging among the biggest manufacturers of construction machinery on the globe, Liebherr also offers high-grade, utility-oriented products and services for other industries as well. The group encompasses more than 150 companies on all continents, employing more than 50,000 people in 2023, who generated consolidated revenues amounting to over 14 billion Euros. Liebherr was established by Hans Liebherr in 1949 in Kirchdorf an der Iller in Southern Germany. Since then, the company’s employees pursue the goal of convincing customers with sophisticated solutions and contributing to technological progress. In 2024, the group is celebrating its 75th anniversary Under the motto “75 years of moving forward”.
Liebherr-Mining Equipment Colmar SAS
49 rue Frédéric Hartmann
CS 50038
68025 Colmar Cedex
France
E-Mail: info.lec@liebherr.com
www.liebherr.com
Publications
Download
Learn more about our products and services
Talk to our embedded computing experts!
Curious about our NXP processor based embedded computing platforms and our system design services? Just ask us! We can't wait to hear from you to help you personally.